Kelly Hose, an integral component in drilling operations, plays a pivotal role in facilitating the transfer of drilling mud between the rig and the drill string.
Understanding its construction, purpose, and maintenance is crucial for ensuring smooth drilling operations.
What Is Kelly Hose
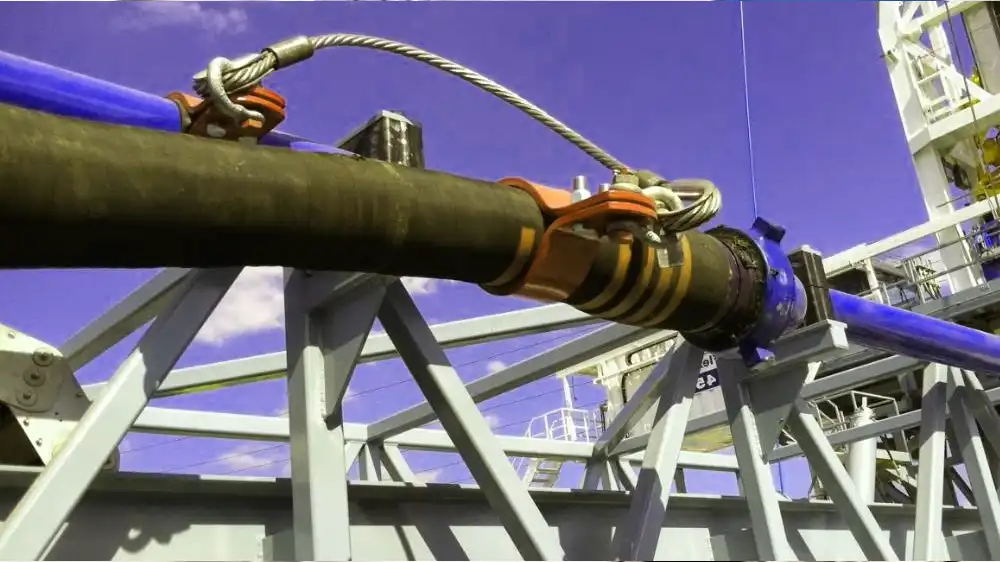
Kelly Hose is a specialized type of flexible, high-pressure hose used in rotary drilling rigs. It connects the standpipe to the swivel, allowing drilling mud to be pumped through the drill string.
Kelly Hose consists of several layers, including an inner tube, reinforcement layers, and an outer cover. These layers are designed to withstand high pressure, abrasion, and harsh environmental conditions encountered during drilling.
Features of Kelly Hose
Kelly Hose, a critical component in drilling operations, boasts several features that make it indispensable in the oil and gas industry. Let’s delve into some of its key attributes:
High Pressure Resistance: One of the primary features of Kelly Hose is its ability to withstand high pressure. Designed to handle the intense hydraulic forces generated during drilling, these hoses are reinforced with layers of durable materials, ensuring they can maintain integrity even under extreme conditions.
Abrasion Resistance: Given the abrasive nature of drilling environments, Kelly Hoses are engineered to resist wear and tear caused by friction with rocks, debris, and other surfaces encountered during drilling operations. This abrasion resistance helps prolong the lifespan of the hose and ensures consistent performance over time.
Flexibility: Flexibility is another essential feature of Kelly Hose, allowing it to bend and maneuver easily around drilling equipment and obstacles. This flexibility enables smooth operation and reduces the risk of kinking or damage to the hose, ensuring uninterrupted mud flow during drilling.
Chemical Compatibility: Kelly Hoses are designed to be compatible with a wide range of drilling fluids and chemicals commonly used in drilling operations. This chemical compatibility prevents degradation of the hose materials and maintains the integrity of the fluid being transported, ensuring optimal drilling performance.
Temperature Resistance: Operating in harsh environments with fluctuating temperatures, Kelly Hoses must withstand both extreme heat and cold. These hoses are engineered to maintain their structural integrity and flexibility across a wide temperature range, ensuring reliable performance in diverse drilling conditions.
Size Variations: Kelly Hoses come in various sizes and lengths to accommodate different rig configurations and drilling requirements. Whether drilling in shallow or deep wells, operators can select the appropriate size and length of hose to suit their specific application, ensuring efficient mud transfer and circulation.
Corrosion Resistance: In addition to withstanding high pressure and abrasion, Kelly Hoses are also resistant to corrosion caused by exposure to corrosive drilling fluids and environmental factors. This corrosion resistance helps maintain the structural integrity of the hose and extends its service life in challenging drilling environments.
Easy Installation and Maintenance: Kelly Hoses are designed for easy installation and maintenance, allowing operators to quickly connect and disconnect them from drilling equipment as needed. Routine maintenance tasks, such as inspection and cleaning, can be performed efficiently, minimizing downtime and optimizing drilling operations.
Importance of Kelly Hose
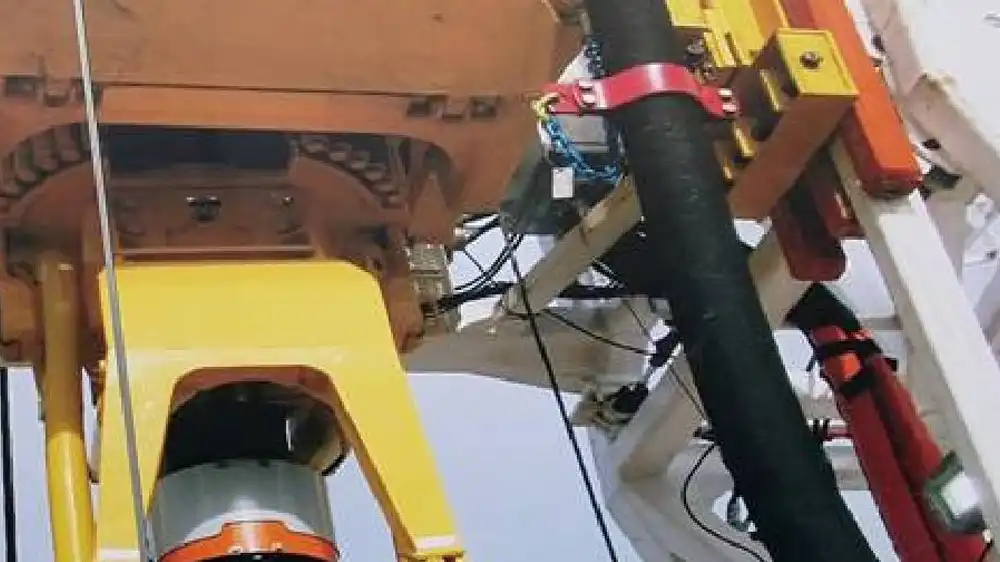
Kelly Hose holds significant importance in the realm of drilling operations, serving as a crucial link between various components of the drilling rig.
Let’s explore why Kelly Hose is indispensable in the oil and gas industry:
Safety Assurance: Ensuring the safety of drilling operations is paramount, and Kelly Hose plays a vital role in this aspect. By facilitating the transfer of drilling mud between the rig and the drill string, Kelly Hose helps maintain proper mud circulation, which is essential for controlling well pressure and preventing blowouts. This contributes to a safer working environment for drilling personnel and helps mitigate the risk of accidents and equipment failures.
Efficiency Enhancement: Efficient drilling operations rely on consistent and uninterrupted mud circulation, and Kelly Hose plays a pivotal role in achieving this objective. By providing a reliable conduit for conveying drilling mud, Kelly Hose enables continuous drilling without disruptions, thereby maximizing productivity and minimizing downtime. This efficiency enhancement translates into cost savings and improved overall operational performance.
Drilling Fluid Management: Drilling mud serves multiple purposes in drilling operations, including lubricating the drill bit, carrying rock cuttings to the surface, and maintaining well stability. Kelly Hose facilitates the efficient transfer of drilling mud to and from the drilling rig, ensuring proper mud management throughout the drilling process. This helps optimize drilling performance and enables operators to achieve desired drilling outcomes with greater precision and control.
Well Control: Maintaining control over wellbore pressure is essential for preventing well control incidents and ensuring the integrity of the well. Kelly Hose plays a critical role in well control by allowing operators to regulate mud flow rates and pressures effectively. This capability helps maintain wellbore stability, prevent formation damage, and minimize the risk of formation fluid influxes, safeguarding the integrity of the well and surrounding environment.
Versatility and Adaptability: Kelly Hoses are available in various sizes, pressure ratings, and configurations to accommodate different drilling requirements and rig specifications. This versatility and adaptability make Kelly Hose suitable for a wide range of drilling applications, from conventional to challenging drilling environments. Whether drilling onshore or offshore, in shallow or deep wells, operators can rely on Kelly Hose to meet their specific operational needs effectively.
Compliance with Regulations: The oil and gas industry is subject to stringent regulatory standards and compliance requirements aimed at ensuring environmental protection, worker safety, and well integrity. Kelly Hose, as an integral component of drilling equipment, must adhere to these regulations and standards to ensure safe and responsible drilling operations. By using certified and compliant Kelly Hoses, operators demonstrate their commitment to upholding industry best practices and regulatory requirements.
In summary, the importance of Kelly Hose in drilling operations cannot be overstated. From enhancing safety and efficiency to facilitating proper drilling fluid management and well control, Kelly Hose plays a crucial role in ensuring the success and sustainability of drilling projects in the oil and gas industry.
Types of Kelly Hoses
There are several types of Kelly Hoses designed to meet the diverse needs of drilling operations. These include:
- Standard Kelly Hose: Suitable for general drilling applications.
- Vibrator Kelly Hose: Specifically designed to withstand high-frequency vibrations encountered during drilling.
- Slim Hole Kelly Hose: Ideal for narrow or confined drilling spaces where standard hoses may not fit.
How to Choose the Right Kelly Hose
Selecting the appropriate Kelly Hose is essential to ensure optimal performance and safety in drilling operations.
Here are some key factors to consider when choosing the right Kelly Hose for your specific needs:
Operating Pressure Requirements: Consider the maximum operating pressure of your drilling system when selecting a Kelly Hose. Choose a hose with a pressure rating that exceeds the maximum pressure encountered during drilling operations to ensure safety and reliability.
Temperature Compatibility: Evaluate the temperature range in which the Kelly Hose will be operating. Ensure that the hose material and construction are compatible with the temperature extremes encountered in your drilling environment to prevent premature degradation or failure.
Fluid Compatibility: Assess the compatibility of the Kelly Hose with the types of drilling fluids and chemicals used in your operations. Choose a hose that is resistant to the specific fluids and additives present in your drilling mud to avoid chemical degradation and contamination.
Size and Length Requirements: Determine the appropriate size and length of the Kelly Hose based on your rig configuration and drilling parameters. Select a hose size that matches the diameter of your drill string and a length that allows for adequate reach and flexibility during operation.
Reinforcement and Construction: Examine the construction and reinforcement layers of the Kelly Hose to ensure durability and longevity. Opt for hoses with robust reinforcement materials, such as high-strength steel wire or synthetic fibers, to withstand high pressures and abrasion encountered in drilling operations.
End Fittings and Connections: Pay attention to the type and compatibility of end fittings and connections on the Kelly Hose. Ensure that the hose is equipped with compatible fittings that securely attach to your rig equipment, preventing leaks or disconnections during operation.
Industry Standards and Certifications: Look for Kelly Hoses that meet industry standards and certifications, such as those set by the American Petroleum Institute (API) or International Organization for Standardization (ISO). Compliance with these standards ensures quality, performance, and safety in accordance with industry best practices.
Consultation with Experts: When in doubt, seek advice from experienced professionals or reputable kelly hose suppliers in the drilling industry. They can provide valuable insights and recommendations based on their expertise and knowledge of Kelly Hose applications and specifications.
Proper Maintenance and Care about Kelly Hose
Maintaining and caring for Kelly Hose is essential to ensure its longevity, performance, and safety in drilling operations. Here are some guidelines for proper maintenance and care:
Regular Inspection: Conduct regular visual inspections of the Kelly Hose before and after each use. Look for signs of wear, damage, or deterioration, such as cuts, abrasions, bulges, or leaks. Pay attention to the hose connections, fittings, and end couplings for any signs of looseness or corrosion.
Pressure Testing: Periodically perform pressure testing on the Kelly Hose to verify its integrity and resistance to high pressures. Use appropriate testing equipment and procedures to ensure accurate results. Replace any hoses that fail to meet pressure testing requirements to prevent potential safety hazards.
Cleaning and Flushing: Clean and flush the Kelly Hose regularly to remove drilling mud, debris, and contaminants that can accumulate inside the hose. Use mild detergent solutions and water to flush out dirt and residues, paying attention to areas where mud tends to accumulate, such as near end connections and fittings.
Avoiding Twisting and Kinking: Handle Kelly Hose with care to avoid twisting, kinking, or bending beyond its specified radius. Improper handling can cause damage to the hose reinforcement layers and compromise its structural integrity. Use hose supports and guides to prevent excessive bending and ensure smooth operation.
Storage and Handling: Store Kelly Hose in a clean, dry, and well-ventilated area away from direct sunlight, heat sources, and harsh chemicals. Avoid sharp edges, rough surfaces, and heavy objects that can cause abrasion or puncture damage to the hose. Use hose racks or reels to prevent tangling and ensure proper storage.
Replacing Worn Components: Replace worn or damaged components of the Kelly Hose, such as end fittings, couplings, and protective covers, as needed. Use genuine replacement parts from reputable manufacturers to maintain compatibility and performance. Inspect and lubricate hose connections regularly to prevent corrosion and ensure tight seals.
Training and Awareness: Provide training to personnel involved in handling and operating Kelly Hose to ensure they understand proper procedures and safety precautions. Emphasize the importance of inspecting, maintaining, and caring for the hose to prevent accidents, injuries, and equipment failures.
Documentation and Records: Maintain detailed records of inspections, maintenance activities, and repairs performed on the Kelly Hose. Keep track of hose usage, operating conditions, and any incidents or issues encountered during drilling operations. Documentation helps identify trends, track performance, and ensure compliance with regulatory requirements.
FAQs about Kelly Hose
What materials are Kelly Hoses made of?
Kelly Hoses are typically made of synthetic rubber reinforced with high-strength steel wire.
How often should Kelly Hoses be inspected?
Kelly Hoses should be inspected regularly, preferably before each use, to identify any signs of wear or damage.
Can Kelly Hoses be customized for specific drilling needs?
Yes, Kelly Hoses can be customized to meet the unique requirements of different drilling operations.
Are there regulations governing the use of Kelly Hoses?
Yes, various industry standards and regulations govern the design, manufacture, and use of Kelly Hoses to ensure safety and reliability.
What is the typical lifespan of a Kelly Hose?
The lifespan of a Kelly Hose depends on factors such as usage, maintenance, and operating conditions but typically ranges from several months to several years.
How do I identify the correct size of Kelly Hose for my equipment?
Consult with a knowledgeable supplier or manufacturer to determine the appropriate size and specifications based on your drilling equipment and operating parameters.
Conclusion
Kelly Hose plays a vital role in the success of drilling operations by facilitating the transfer of drilling mud and maintaining rig safety. Understanding its construction, selection criteria, and maintenance requirements is essential for ensuring efficient and safe drilling activities.
For further information on Kelly Hose and related products, refer to reputable industry sources and consult with experienced professionals.