In the dynamic and demanding environment of the oil and gas industry, the proper handling and maintenance of oilfield hoses are crucial for ensuring worker safety, operational efficiency, and equipment longevity. These specialized hoses play a vital role in the transfer of a variety of fluids and gases, from drilling mud to high-pressure steam, and their failure can have serious consequences.
In this comprehensive blog post, we will explore the best practices and essential tips for the safe and effective handling of oilfield hoses, equipping you with the knowledge to optimize their performance and extend their lifespan.
What Is Oilfield Hose
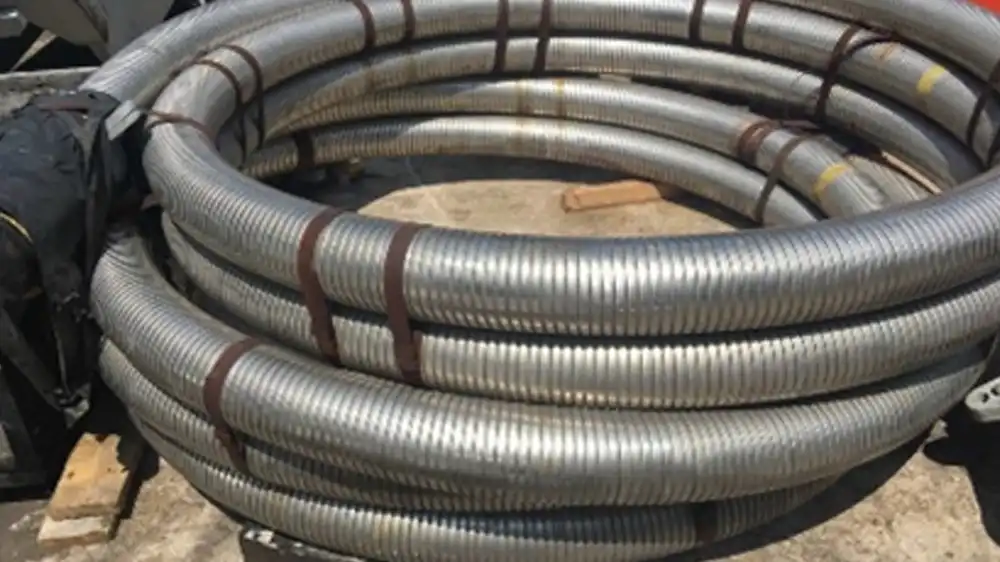
Oilfield hoses are specialized, high-performance hoses used in the oil and gas industry to transport a variety of fluids and gases. These hoses are designed to withstand the demanding conditions found in oilfield operations, including high pressures, abrasive materials, and extreme temperatures.
Some key features and applications of oilfield hoses include:
- Drilling Mud Hoses: Used to transport drilling fluids (mud) from the mud pumps to the drill string, these hoses must be able to handle high pressures and resist abrasion from the drilling mud.
- Hydraulic Hoses: Responsible for powering hydraulic systems on drilling rigs, well servicing equipment, and other oilfield machinery. These hoses need to withstand high pressures and maintain flexibility.
- Suction and Discharge Hoses: Utilized for the transfer of liquids and gases, such as oil, water, and natural gas, between various equipment and storage tanks.
- Casing and Tubing Hoses: Employed in the installation and removal of casing and tubing during well operations, these hoses must be durable and flexible to navigate the challenging oilfield terrain.
- Steam Hoses: Used to transport high-pressure steam for well stimulation, enhanced oil recovery, and other thermal applications.
Oilfield hoses are typically made from materials such as rubber, thermoplastic, or a combination of materials, depending on the specific requirements of the application. These hoses are designed to resist abrasion, chemicals, and high temperatures, ensuring reliable and safe fluid and gas transfer in the oilfield environment.
Proper handling, maintenance, and replacement of oilfield hoses are crucial to ensure worker safety, operational efficiency, and equipment longevity. Adhering to industry best practices and regulatory standards is essential for managing these critical components of oilfield operations.
Oilfield Hose Types and Applications
Oilfield hoses come in a wide range of sizes, materials, and configurations to meet the diverse demands of the industry. Some of the most common types of oilfield hoses include:
- Drilling Mud Hoses: Used to transport drilling fluids from the mud pumps to the drill string, these hoses must withstand high pressures and abrasive conditions.
- Hydraulic Hoses: Responsible for powering various hydraulic systems, such as those used in drilling rigs and well servicing equipment, these hoses require careful handling to maintain their integrity.
- Suction and Discharge Hoses: Utilized for the transfer of liquids and gases, these hoses must be compatible with the specific fluids or gases they are handling.
- Casing and Tubing Hoses: Employed in the installation and removal of casing and tubing, these hoses need to be durable and flexible to navigate the challenging oilfield terrain.
Understanding the specific application and requirements of each hose type is essential for developing appropriate handling and maintenance protocols.
Oilfield Hoses Handling Tips
Inspect Hoses Regularly:
- Visually inspect hoses for any signs of wear, damage, or deterioration before each use.
- Check for cracks, cuts, abrasions, or bulges in the hose casing.
- Ensure the couplings are securely attached and not damaged.
Avoid Kinking or Bending:
- Do not kink or bend the hose beyond its minimum bend radius, as this can damage the internal structure and lead to premature failure.
- Use appropriate hose guides, rollers, or supports to maintain the proper bend radius during operation.
Proper Storage and Transport:
- Store hoses in a cool, dry, and well-ventilated area, away from direct sunlight and heat sources.
- Avoid dragging or dropping hoses, as this can cause damage to the outer cover and internal reinforcement.
- Transport hoses using appropriate vehicles or equipment to prevent damage during movement.
Avoid Excessive Pressure and Temperature:
- Do not exceed the maximum working pressure or temperature ratings specified by the hose manufacturer.
- Monitor pressure and temperature throughout the operation to ensure they remain within the safe operating limits.
Proper Handling Techniques:
- Use appropriate personal protective equipment (PPE), such as gloves, when handling hoses to prevent injuries.
- Lift and move hoses using proper lifting techniques to avoid strains or back injuries.
- Avoid stepping on or running over hoses, as this can damage the outer cover and internal reinforcement.
Maintain Cleanliness:
- Keep hoses clean and free from contaminants, such as dirt, debris, or chemicals, to prevent premature wear and deterioration.
- Use appropriate cleaning methods and materials recommended by the hose manufacturer.
Proper Coupling and Connections:
- Ensure couplings and connections are properly aligned and securely tightened to prevent leaks or disconnections.
- Follow the manufacturer‘s instructions for coupling and connection procedures.
Replacement and Retirement:
- Replace hoses according to the manufacturer‘s recommendations or when signs of significant wear or damage are observed.
- Properly dispose of retired hoses in accordance with environmental regulations and guidelines.
By following these tips, you can help ensure the safe and efficient operation of oilfield hoses, extend their service life, and maintain a safe working environment.
Regulatory Compliance and Safety Considerations (continued)
- Pressure and Temperature Ratings: Strictly adhere to the manufacturer‘s specified pressure and temperature ratings for each hose to prevent catastrophic failures and ensure the safety of personnel.
- Hazardous Material Handling: When dealing with hoses that transport hazardous materials, such as flammable liquids or corrosive chemicals, follow all applicable regulations and implement appropriate safety protocols.
- Training and Competency: Provide comprehensive training to all personnel involved in the handling, maintenance, and operation of oilfield hoses, ensuring they are competent in the safe and proper procedures.
- Incident Reporting and Investigation: Establish a robust system for reporting and investigating any incidents or near-misses related to oilfield hose failures or mishandling, allowing for the implementation of corrective actions and continuous improvement.
By staying up-to-date with regulatory requirements and prioritizing safety, you can minimize the risks associated with oilfield hose handling and create a work environment that protects both your personnel and your valuable equipment.
Proactive Maintenance and Replacement Strategies
Implementing a proactive maintenance and replacement strategy for your oilfield hoses is essential for maximizing their performance and longevity. This approach involves:
- Scheduled Inspections: Conduct regular, scheduled inspections of your hoses, checking for signs of wear, damage, or deterioration. Document the findings and maintain detailed records.
- Preventive Maintenance: Develop a comprehensive preventive maintenance program that includes cleaning, lubrication, and the replacement of worn or damaged components, as recommended by the manufacturer.
- Replacement Guidelines: Establish clear guidelines for the replacement of oilfield hoses, considering factors such as age, usage, and the results of inspections and pressure tests.
- Inventory Management: Maintain a well-stocked inventory of replacement hoses and components to ensure prompt availability when needed, minimizing downtime and operational disruptions.
- Traceability and Documentation: Implement a system for tracking the history and performance of each oilfield hose, including its installation, maintenance, and replacement, to inform future decision-making.
By adopting a proactive approach to oilfield hose maintenance and replacement, you can:
- Extend the useful life of your hoses
- Reduce the risk of unexpected failures and unplanned downtime
- Optimize operational efficiency and cost-effectiveness
- Demonstrate compliance with industry standards and regulations
Investing in a robust maintenance program for your oilfield hoses is a strategic decision that can pay dividends in terms of improved safety, reliability, and overall asset management.
Conclusion
In the dynamic and demanding oilfield environment, the proper handling and maintenance of hoses are essential for ensuring worker safety, operational efficiency, and equipment longevity. By understanding the various types of oilfield hoses and their specific applications, adhering to best practices for handling, and implementing proactive maintenance strategies, you can optimize the performance and lifespan of these critical components.
Staying up-to-date with regulatory requirements, prioritizing safety, and fostering a culture of continuous improvement are also key to effectively managing your oilfield hose assets. By embracing these principles, you can contribute to the overall success and sustainability of your oilfield operations.