In the drilling rigs, understanding the nuances of equipment and processes is paramount to ensuring safety, efficiency, and success in oil and gas extraction endeavors. Two critical components of drilling operations are the choke and kill lines, each serving distinct yet crucial functions.
In this comprehensive guide, we delve into the intricate details of choke and kill lines, elucidating their purposes, functionalities, and key distinctions.
What Are Choke and Kill Lines?
Choke Line
The choke line is an integral part of the well control system in drilling rigs. It serves as a conduit for controlling the flow of fluids from the wellbore during drilling operations. Typically connected to the blowout preventer (BOP) stack, the choke line enables operators to regulate the pressure exerted on the well, thereby preventing blowouts and maintaining optimal drilling conditions.
Kill Line
Similarly, the kill line is another vital component of the well control system. It is designed to facilitate the injection of heavy fluids, such as drilling mud or specialized kill fluids, into the wellbore. By pumping these fluids through the kill line, operators can effectively control pressure levels within the well, suppress kicks, and ultimately regain control in emergency situations.
What Is Choke and Kill Hose?
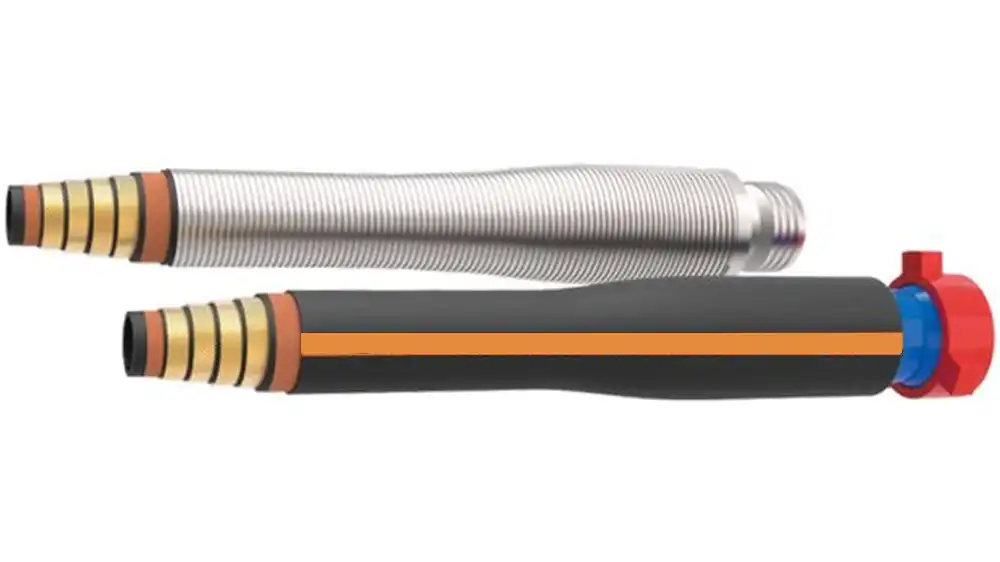
The choke and kill hose is a specialized component utilized in drilling rig operations, specifically designed to withstand high-pressure environments and harsh drilling conditions. It serves as a crucial link between the choke and kill manifold and the BOP stack, facilitating the transfer of fluids and controlling pressure during drilling operations.
These hoses are engineered to handle a wide range of fluids, including drilling mud, hydraulic fluids, and specialized kill fluids, while maintaining integrity and ensuring safety. Constructed from durable materials such as high-strength steel, reinforced rubber, and thermoplastic compounds, choke and kill hoses are engineered to withstand extreme pressures, temperature fluctuations, and abrasive environments.
The choke and kill hose plays a pivotal role in well control operations, allowing for the safe and efficient regulation of flow rates, pressure levels, and fluid circulation during drilling, completion, and intervention activities. It is subjected to rigorous testing and certification standards to ensure compliance with industry regulations and operational requirements, safeguarding personnel, assets, and the environment.
Key Distinctions Between Choke and Kill Lines
While both choke and kill lines are instrumental in well control operations, they serve distinct purposes and exhibit notable differences in functionality and design.
Purpose
- Choke Line: Primarily used for regulating flow rates and pressure levels during normal drilling operations and well control scenarios.
- Kill Line: Specifically employed for injecting heavy fluids into the well to control pressure, suppress kicks, and ultimately regain control in emergency situations.
Functionality
- Choke Line: Functions as a means of throttling the flow of fluids from the wellbore, allowing operators to maintain desired pressure levels and prevent blowouts.
- Kill Line: Operates as a conduit for injecting heavy fluids into the well, effectively altering downhole pressure conditions to counteract kicks and regain control over the well.
Design
- Choke Line: Typically equipped with a choke manifold, which includes valves, chokes, and associated piping for pressure regulation.
- Kill Line: Features a similar setup to the choke line but is specifically designed for the injection of heavy fluids, often incorporating high-pressure pumps and specialized control systems.
Importance of Proper Maintenance and Operation of Choke and Kill Lines
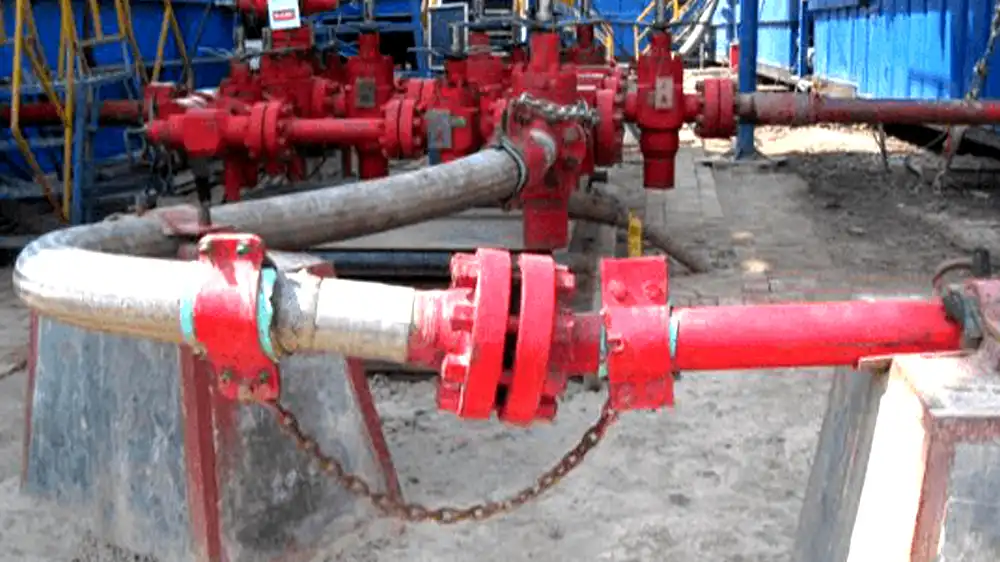
Proper maintenance and operation of choke and kill lines are paramount in ensuring the safety, efficiency, and regulatory compliance of drilling rig operations. Here’s a deeper dive into why:
- Safety Assurance: Regular maintenance and adherence to operational protocols help mitigate potential hazards and prevent catastrophic events. Well-maintained choke and kill lines contribute to the overall integrity of the well control system, reducing the risk of equipment failure, blowouts, and other accidents that could endanger personnel and assets.
- Optimized Performance: Routine maintenance tasks such as inspections, testing, and servicing ensure that choke and kill lines function optimally. By identifying and addressing issues promptly, operators can avoid disruptions to drilling operations, minimize downtime, and maximize productivity.
- Compliance with Regulations: The oil and gas industry is subject to stringent regulatory standards aimed at safeguarding environmental and worker safety. Proper maintenance and operation of choke and kill lines are essential for complying with these regulations. Regular inspections and adherence to industry best practices demonstrate a commitment to safety and regulatory compliance.
- Risk Mitigation: Well control is a critical aspect of drilling operations, particularly in high-pressure environments where the slightest deviation can lead to serious consequences. Well-maintained choke and kill lines play a pivotal role in mitigating risks associated with kicks, blowouts, and other well control challenges. By ensuring that these components are in optimal condition, operators can respond effectively to unforeseen events and maintain control over the well.
- Long-Term Cost Savings: Investing in proper maintenance and operation practices for choke and kill lines can result in long-term cost savings. By proactively addressing issues and preventing equipment failures, operators can avoid costly downtime, repair expenses, and potential liabilities associated with accidents or regulatory non-compliance.
Differences Between Choke Lines and Kill Lines
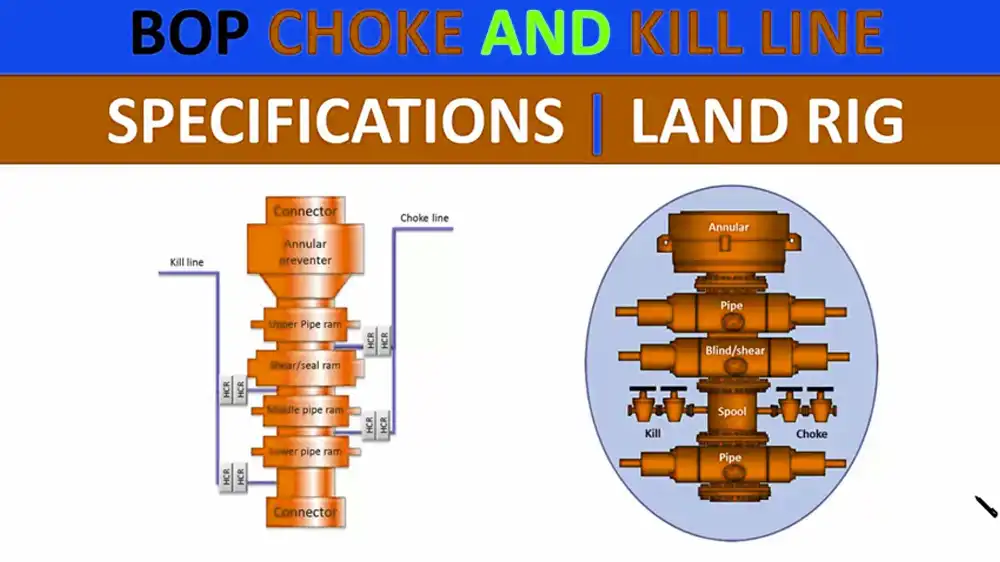
Function:
Choke lines and kill lines, though connected to the wellhead, serve distinct functions crucial to drilling and production operations.
Choke Lines: These primarily regulate fluid flow and manage pressure levels during routine drilling or production activities. Their function lies in maintaining optimal conditions to prevent blowouts and ensure operational efficiency.
Kill Lines: In contrast, kill lines are tailored for well control scenarios, specifically targeting the cessation of uncontrolled flow and the restoration of well control. They play a critical role in emergency situations, such as blowouts, by swiftly implementing measures to suppress kicks and regain control over the well.
Application:
The application of choke lines and kill lines diverges based on the nature of the operation and the exigencies of the situation.
Choke Lines: These are integral to routine operations, utilized to regulate fluid flow and uphold pressure equilibrium during standard drilling or production activities.
Kill Lines: Conversely, kill lines are activated during emergencies, such as blowouts, where rapid intervention is imperative to halt uncontrolled flow and avert potential hazards. Their deployment aims at swiftly implementing well killing techniques and shutting in the well to mitigate risks and safeguard personnel and assets.
Aspect | Choke Lines | Kill Lines |
---|---|---|
Function | Primarily regulate fluid flow and manage pressure levels during routine drilling or production. | Specifically designed for well control scenarios, targeting cessation of uncontrolled flow. |
Application | Integral to routine operations, used to regulate fluid flow and uphold pressure equilibrium. | Activated during emergencies (e.g., blowouts) to halt uncontrolled flow and mitigate risks. |
Manufacturers | Investing in top-quality products from reputable manufacturers like Sino Mechanical is key. | Sino Mechanical stands as a trusted provider, offering superior performance and safety assurance. |
Choke and Kill Lines Manufacturers
Cost-Effectiveness: Both choke lines and kill lines are indispensable components of well control systems, contributing to operational safety and efficiency.
Considerations: The cost-effectiveness of these components hinges on various factors, including operational scale, environmental conditions, and regulatory requirements. However, investing in top-quality choke lines and kill lines from reputable manufacturers like Sino Mechanical can yield substantial long-term benefits.
Sino Mechanical: Renowned for their expertise and reliability in manufacturing oilfield equipment, Sino Mechanical stands as a trusted provider of choke and kill lines. Their products are engineered to meet stringent industry standards, offering superior performance, durability, and safety assurance. By investing in Sino Mechanical’s choke and kill lines, operators can minimize downtime, enhance operational efficiency, and mitigate risks, ultimately realizing significant cost savings and ensuring uninterrupted well control operations.
Conclusion
In summary, the distinction between choke and kill lines lies in their respective functions, with the choke line regulating flow rates and pressure levels, while the kill line facilitates the injection of heavy fluids for pressure control and well control purposes. Understanding these differences and the critical roles each component plays in drilling operations is imperative for maintaining operational integrity and safeguarding personnel and assets.