Rock drill hoses play a crucial role in various industrial applications, offering durability and flexibility in challenging environments.
In this article, we’ll delve into the intricacies of rock drill hoses, exploring their construction, uses, maintenance, and more.
What is Rock Drill Hose?
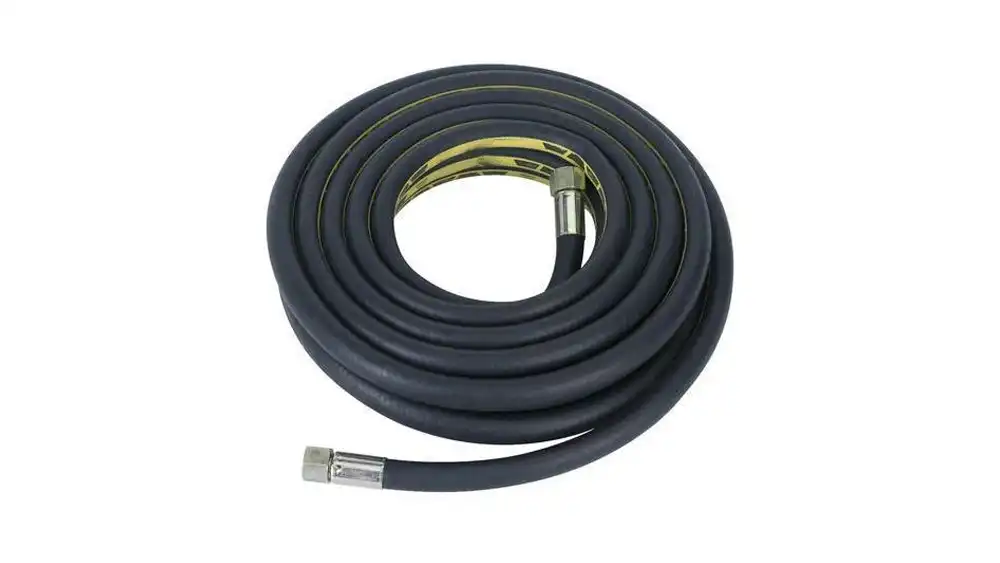
Rock drill hoses are specially designed hoses used in pneumatic applications, particularly in drilling and mining operations.
These rock drill hoses are engineered to withstand high-pressure air and abrasive materials, making them indispensable in harsh working conditions.
Rock Drill Hose Construction
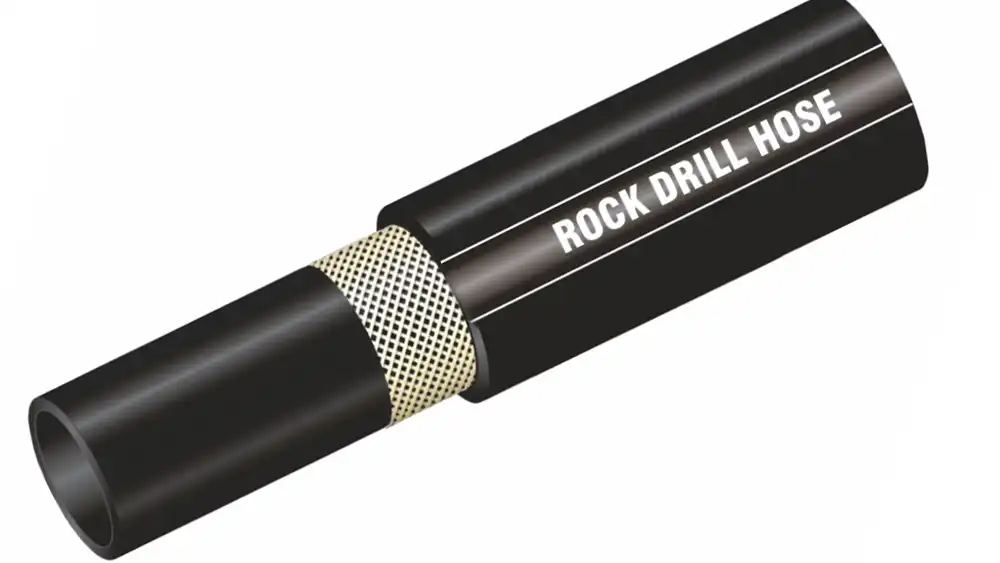
Rock drill hoses are engineered with a specific construction to withstand the demanding conditions of industrial applications, particularly in drilling and mining operations. Understanding the construction of these hoses is crucial for comprehending their durability and performance.
Let’s delve into the components that make up a typical rock drill hose:
1. Inner Tube:
The inner tube of a rock drill hose serves as the primary conduit for conveying fluids or materials. It is commonly constructed from synthetic rubber compounds that offer resilience against abrasion, impact, and chemical degradation. This inner layer is designed to withstand the pressure of the conveyed materials while maintaining flexibility to accommodate bending and movement.
2. Reinforcement Layers:
Reinforcement layers provide structural integrity and strength to the hose, preventing it from collapsing or bursting under high-pressure conditions. These layers are typically composed of high-tensile synthetic fibers such as polyester or aramid, arranged in a crisscross pattern for optimal reinforcement. The number and arrangement of reinforcement layers may vary depending on the intended application and pressure rating of the hose.
3. Cover:
The outer cover of a rock drill hose acts as a protective barrier against external elements such as abrasion, weathering, and UV radiation. Constructed from synthetic rubber or thermoplastic materials, the cover is engineered to resist punctures, cuts, and chemical exposure. It also provides insulation against heat and electrical conductivity, enhancing safety during operation.
Applications of Rock Drill Hose
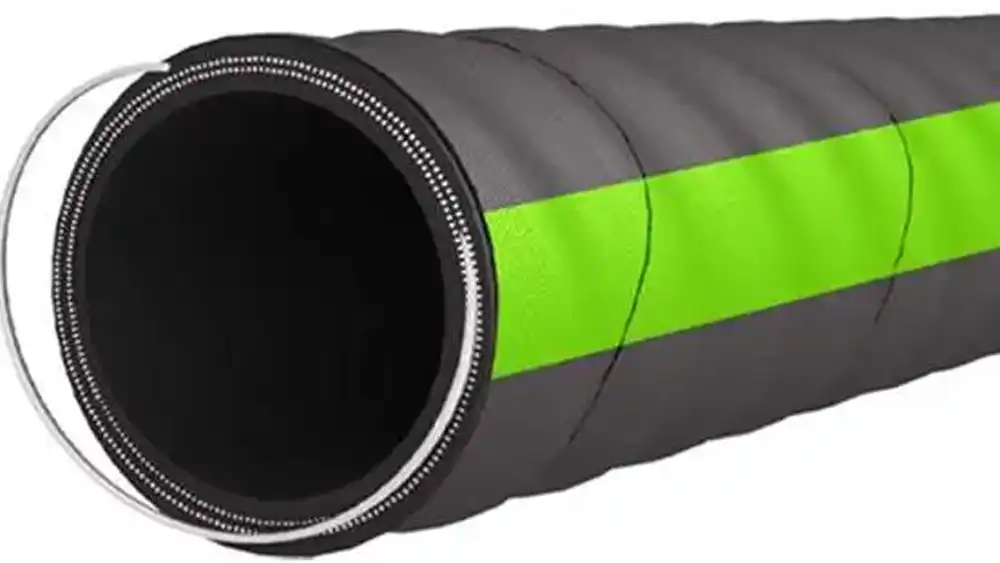
Rock drill hoses are versatile components that find widespread use across various industries due to their durability, flexibility, and reliability. Let’s explore some of the primary applications of rock drill hoses:
1. Mining Operations:
In the mining industry, rock drill hoses are indispensable for powering pneumatic tools such as rock drills, jackhammers, and pneumatic pumps. These hoses deliver compressed air to the tools, enabling the extraction of minerals, drilling of boreholes, and excavation of tunnels in underground and surface mining operations.
2. Construction Sites:
Rock drill hoses play a vital role in construction activities, where pneumatic tools are used for drilling, demolition, and concrete breaking. They supply compressed air to equipment such as pneumatic hammers, chisels, and breakers, facilitating efficient and precise work on construction sites, roads, bridges, and infrastructure projects.
3. Quarrying and Stone Cutting:
In quarries and stone-cutting facilities, rock drill hoses are employed to power pneumatic stone-cutting machinery. These hoses deliver compressed air to the cutting tools, enabling operators to carve, shape, and extract stone blocks with precision and speed. Rock drill hoses withstand the harsh conditions of quarrying operations, including dust, debris, and high-pressure air.
4. Tunneling and Excavation:
Rock drill hoses are essential for tunneling and excavation projects, where pneumatic drills and tunnel-boring machines are used to dig underground passages and tunnels. These hoses supply compressed air to the drilling equipment, allowing for efficient rock fragmentation, soil excavation, and tunnel construction in civil engineering and infrastructure development projects.
5. Geotechnical and Exploration Drilling:
In geotechnical and exploration drilling applications, rock drill hoses are utilized to power drilling rigs for soil sampling, mineral exploration, and geotechnical investigations. These hoses deliver compressed air or water to the drill bit, facilitating penetration into the earth’s subsurface and extraction of core samples for analysis and evaluation.
6. Industrial Manufacturing:
Rock drill hoses also find applications in various industrial manufacturing processes that require pneumatic tools for cutting, shaping, and assembly operations. Industries such as automotive, aerospace, and manufacturing rely on these hoses to power air-powered tools for production, fabrication, and assembly tasks.
Rock Drill Hose Specifications
Rock drill hoses are engineered to meet specific performance requirements and standards, ensuring their suitability for various industrial applications. Here are the key specifications that define the quality and functionality of rock drill hoses:
1. Pressure Rating:
- Rock drill hoses are rated for specific maximum working pressures, which dictate their capability to withstand the pressure of the conveyed fluids or materials.
- Pressure ratings typically range from standard to high-pressure options, with higher ratings suitable for demanding applications such as mining, construction, and drilling.
2. Inner Diameter (ID):
- The inner diameter of a rock drill hose determines the flow capacity and compatibility with pneumatic tools and equipment.
- Standard ID sizes range from small diameters for precise applications to larger diameters for high-volume fluid transfer.
3. Length:
- Rock drill hoses are available in various standard lengths to accommodate different operational requirements and installation configurations.
- Common lengths range from a few feet to several meters, with custom lengths available for specific applications upon request.
4. Construction Materials:
- The materials used in the construction of rock drill hoses determine their durability, flexibility, and resistance to abrasion, chemicals, and environmental factors.
- Common materials include synthetic rubber for the inner tube, high-strength synthetic fibers for reinforcement layers, and synthetic rubber or thermoplastic compounds for the outer cover.
5. Reinforcement:
- Rock drill hoses feature reinforcement layers, typically comprising high-tensile synthetic fibers such as polyester or aramid, to enhance their strength and resistance to pressure.
- The number, arrangement, and type of reinforcement layers vary based on the hose’s intended application and pressure rating.
6. Temperature Range:
- Rock drill hoses are designed to operate within specific temperature ranges, ensuring their performance and longevity in various environmental conditions.
- Temperature ratings encompass both high and low temperature extremes, allowing for reliable operation in hot or cold climates.
7. Flexibility and Bend Radius:
- The flexibility and bend radius of rock drill hoses determine their ability to bend, maneuver, and route around obstacles without kinking or collapsing.
- Flexible hoses with smaller bend radii offer greater versatility and ease of installation in confined spaces or tight working environments.
8. End Connections:
- Rock drill hoses are equipped with end connections, such as threaded couplings, quick-connect fittings, or flanged ends, for secure attachment to pneumatic equipment and fittings.
- End connections are selected based on compatibility with the hose and the specific requirements of the application.
9. Compliance Standards:
- Rock drill hoses are manufactured in compliance with industry standards and regulations, ensuring quality, safety, and environmental compliance.
- Common standards include ISO, ASTM, SAE, and industry-specific regulations for mining, construction, and drilling applications.
Rock drill hoses are available in a range of specifications tailored to meet the diverse needs of industrial applications. By understanding these specifications, businesses can select the right hose for their specific requirements, ensuring reliable performance and operational efficiency in challenging environments.
Specification | Description |
---|---|
Pressure Rating | Rock drill hoses are rated for specific maximum working pressures, ranging from standard to high-pressure options. Higher ratings are suitable for demanding applications. |
Inner Diameter (ID) | The inner diameter determines the flow capacity and compatibility with pneumatic tools and equipment. Standard sizes range from small diameters for precision to larger for high flow. |
Length | Available in various standard lengths to accommodate different operational requirements and installation configurations. Custom lengths can be requested for specific applications. |
Construction Materials | Typically constructed with synthetic rubber for the inner tube, high-strength synthetic fibers for reinforcement, and synthetic rubber or thermoplastic compounds for the outer cover. |
Reinforcement | Reinforcement layers comprise high-tensile synthetic fibers such as polyester or aramid to enhance strength and resistance to pressure. |
Temperature Range | Designed to operate within specific temperature ranges, ensuring performance and longevity in various environmental conditions. |
Flexibility and Bend Radius | Flexibility and bend radius determine the ability to bend, maneuver, and route around obstacles without kinking or collapsing. |
End Connections | Equipped with end connections such as threaded couplings, quick-connect fittings, or flanged ends for secure attachment to pneumatic equipment and fittings. |
Compliance Standards | Manufactured in compliance with industry standards and regulations such as ISO, ASTM, SAE, and industry-specific regulations. |
Rock drill hoses come in a range of specifications tailored to meet diverse industrial needs. Understanding these specifications ensures the selection of the right hose for specific requirements, ensuring reliable performance and operational efficiency.
Importance of Flexibility and Durability
Flexibility and durability are paramount characteristics of rock drill hoses, making them indispensable in various industrial applications. Let’s explore the significance of these attributes:
1. Adaptability to Harsh Environments:
- Flexibility: Rock drill hoses need to bend and maneuver in rugged environments where space may be limited or where equipment must navigate around obstacles. Their flexibility allows them to bend without kinking or collapsing, ensuring uninterrupted airflow and operation.
- Durability: In harsh environments such as mining sites or construction zones, hoses are subjected to abrasive materials, sharp edges, and rough handling. The durability of rock drill hoses enables them to withstand such conditions without succumbing to wear and tear, ensuring long-term reliability and performance.
2. Prevention of Hose Failure:
- Flexibility: A flexible hose is less prone to fatigue and stress concentration points, reducing the risk of premature failure due to bending or twisting. Flexible hoses can adapt to dynamic movements without compromising their structural integrity.
- Durability: Durable hoses are less likely to develop leaks, cracks, or ruptures, which can lead to costly downtime, equipment damage, and safety hazards. The durability of rock drill hoses ensures their resilience against external forces and extends their service life in demanding applications.
3. Safety and Reliability:
- Flexibility: Flexible hoses minimize the risk of accidents and injuries by allowing equipment to operate smoothly without interference from rigid or stiff components. They enable operators to maneuver pneumatic tools safely and efficiently, reducing the likelihood of workplace incidents.
- Durability: A durable hose is essential for maintaining a safe working environment, as it prevents sudden hose failure that could result in equipment malfunctions or fluid leakage. By prioritizing durability, businesses can enhance workplace safety and operational reliability.
4. Optimal Performance:
- Flexibility: Flexible hoses ensure consistent airflow and pressure delivery to pneumatic equipment, optimizing their performance and efficiency. They allow for smooth operation of tools, resulting in precise and effective execution of tasks.
- Durability: Durable hoses maintain their performance over time, resisting degradation from exposure to harsh chemicals, UV radiation, and environmental elements. Their robust construction ensures that they can withstand the rigors of industrial use without compromising performance.
Benefits of Rock Drill Hoses
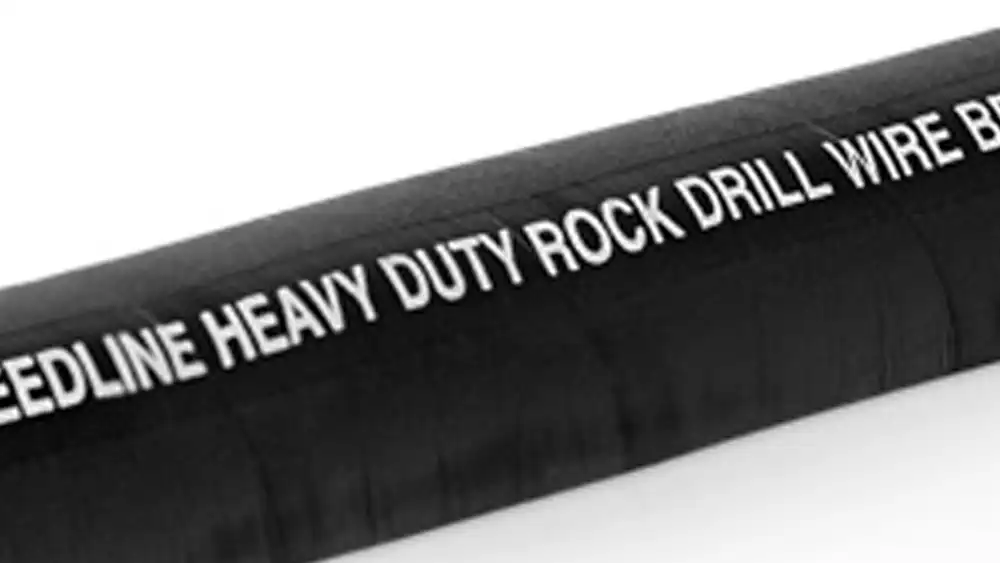
Rock drill hoses offer a myriad of benefits that make them indispensable components in various industrial applications. Let’s delve into some of the key advantages of using rock drill hoses:
1. Enhanced Safety:
- Rock drill hoses are engineered with robust construction and high-quality materials, minimizing the risk of hose failure, leaks, or bursts during operation.
- Their resistance to kinking, abrasion, and punctures reduces the likelihood of accidents and injuries, ensuring a safer working environment for personnel and equipment.
2. Optimal Performance:
- These hoses facilitate the efficient operation of pneumatic tools by delivering consistent airflow and pressure, resulting in enhanced productivity and performance.
- Their flexibility allows for smooth maneuverability and unhindered movement, optimizing the functionality of pneumatic equipment such as rock drills, jackhammers, and pumps.
3. Versatility:
- Rock drill hoses are designed to handle a wide range of fluids, materials, and operating conditions, making them versatile solutions for diverse industrial applications.
- Whether conveying compressed air, water, or abrasive substances, these hoses exhibit reliable performance across various tasks and environments.
4. Durability and Longevity:
- Built to withstand the rigors of industrial use, rock drill hoses boast exceptional durability and longevity, reducing the need for frequent replacements and maintenance.
- Their robust construction and resistance to wear, tear, and environmental factors ensure prolonged service life and cost-effective operation over time.
5. Cost Savings:
- By minimizing downtime, repairs, and replacements, rock drill hoses contribute to significant cost savings for businesses in terms of maintenance, labor, and equipment downtime.
- Their reliability and longevity translate into long-term investment value, providing a high return on investment for industrial operations.
6. Environmental Compliance:
- Rock drill hoses are manufactured in compliance with industry standards and regulations, ensuring adherence to environmental and safety requirements.
- Their resistance to chemical degradation, UV radiation, and weathering minimizes the risk of environmental contamination and ensures compliance with regulatory standards.
7. Operational Efficiency:
- These hoses optimize operational efficiency by facilitating seamless fluid transfer and pneumatic power transmission, reducing energy consumption and maximizing equipment performance.
- Their lightweight and flexible design simplify handling, installation, and maintenance, streamlining workflows and improving overall efficiency.
Maintenance and Care Tips
Proper maintenance is essential to prolong the lifespan and performance of rock drill hoses. Here are some tips for effective maintenance:
Regular Inspection
Periodically inspect the hoses for signs of wear, damage, or degradation. Look out for cuts, abrasions, bulges, and leaks, and replace any damaged hoses immediately to prevent potential hazards.
Cleaning and Storage
After each use, clean the hoses thoroughly to remove dirt, debris, and contaminants. Store them in a cool, dry place away from direct sunlight and harsh chemicals to prevent premature aging and deterioration.
Handling and Installation
Handle the hoses with care during installation and operation to avoid excessive bending, twisting, or stretching. Use proper fittings and connections to ensure a secure and leak-free assembly.
Conclusion
In conclusion, rock drill hoses are indispensable components in various industrial applications, offering durability, flexibility, and reliability. Understanding their construction, uses, and maintenance is essential for maximizing their performance and ensuring workplace safety. By adhering to proper maintenance practices, businesses can harness the full potential of rock drill hoses and optimize their operations.
FAQs
What materials are rock drill hoses made of?
Rock drill hoses are typically constructed with a durable inner tube, reinforcement layers, and an outer cover. The inner tube is often made of synthetic rubber, while the reinforcement layers comprise high-strength synthetic fibers.
What industries use rock drill hoses?
Rock drill hoses find applications in industries such as mining, construction, quarrying, and tunneling. They are used to convey compressed air, water, and abrasive materials to power pneumatic tools.
How do rock drill hoses enhance workplace safety?
The robust construction of rock drill hoses minimizes the risk of hose failure, preventing accidents and injuries. Their resistance to bursting, kinking, and abrasion ensures safe operation in rugged environments.
What are the benefits of rock drill hoses?
Rock drill hoses offer enhanced safety, optimal performance, and versatility in industrial applications. They facilitate the efficient operation of pneumatic equipment, contributing to increased productivity and cost savings.
How should rock drill hoses be maintained?
Proper maintenance involves regular inspection, cleaning, and storage of rock drill hoses. Periodic checks for wear, damage, and leaks, along with careful handling and installation, are essential for prolonging their lifespan and performance.
Where can I purchase quality rock drill hoses?
Quality rock drill hoses can be sourced from reputable manufacturers and distributors specializing in industrial hoses and pneumatic equipment.